-
1. PVD coating: Optimize production efficiency by reducing color change times
In the world of blow molding, precision and speed are crucial factors. With the aim of maximizing production capacity and reducing the cost of operations, Techne Packaging has implemented the treatment of Physical Vapor Deposition (PVD), a quick die head coating solution.
In this article we unveil the importance of PVD for rapid color change, examining how this technology not only accelerates color change processes, but also sets a new standard for efficiency, quality and versatility.
2. What is PVD coating technology?
PVD, or Physical Vapor Deposition is a coating that is applied to the extrusion head of the blow molding machine. Its function is to improve the smoothness of plastic on metal, reducing the adhesion effect and facilitating faster color change.
Unveiling the power of PVD coating technology
The PVD coating treatment involves the deposition of 1200 alternating layers of Chromium Nitride (CrN) and Niobium Nitride (NbN) onto the die head. This results in a surface with a hardness exceeding 2500Hv and a low coefficient of friction (0.4). The high-performance coating is applied at 280°C (536 degrees Fahrenheit), making it applicable to various mechanical and molding applications with temperatures below 850°C (1562 degrees Fahrenheit).
Versatility and compliance
One notable advantage of Techne's PVD solution is its applicability to different metal substrates at low temperatures. Moreover, it complies with safety standards, being suitable for both food contact and medical device applications, meeting ISO 10993-5:2009 and REG EU 1935/2004 requirements.
Maximizing production capacity and efficiency
Techne Packaging ensures a quicker changeover, leading to a reduction in production downtime during color changes. Additionally, the coating minimizes the adhesion of plastic material to metal surfaces, resulting in fewer cleaning interventions. This not only improves efficiency but also reduces operational costs, making it a strategic choice for blow molders.
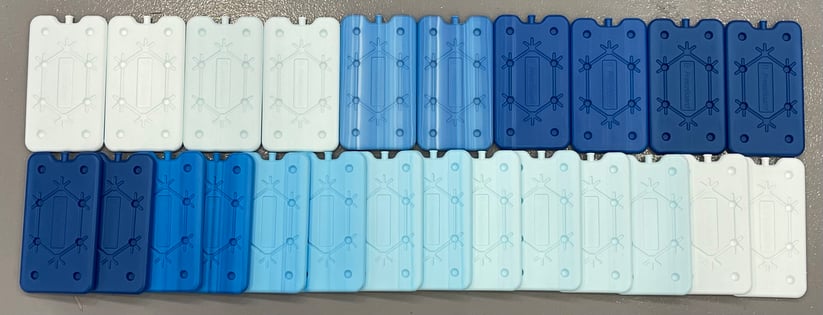
3. PVD coating: Which are the main features?
The consequences and benefits of implementing PVD coating in the blow molding machine are many.
Below are the main ones:
- Fast color change: The PVD treatment reduces the time required for color change of containers.
- Improved smoothness: The PVD treatment improves the smoothness of the polymer on the metal, reducing adherence effect and facilitating a fast color change.
- Reduction of cleaning operations: Due to better smoothness of the polymer on the metal, cleaning operations are also reduced.
- Mold surface protection: The PVD is a coating and surface treatment solution that ensures mold surface protection, greater wear resistance and lower friction.
- Better packaging finish: PVD coating protects the physical properties of the mold surface, this also helps to improve consequently the finish of the molded packaging.
- Deposition temperature: The treatment of PVD coating deposits at 280°C or 536 degrees Fahrenheit. It can be employed in various applications, either mechanical or molding, with temperatures below 850°C or 1562 degrees Fahrenheit.
- Versatility: Suitable for any type of metal substrate if deposited at low temperatures.
- Compliance: Suitable for both food contact and use on medical devices, according to ISO 10993-5:2009 plus REG EU 1935/2004.
If you have already made up your mind on what kind of coating you want for your bottle packaging and want to know more, download the datasheet.
Leave a comment